Scientists just made a huge breakthrough in reducing plastic waste
We may have just figured out a way to make plastic part of an energy future.
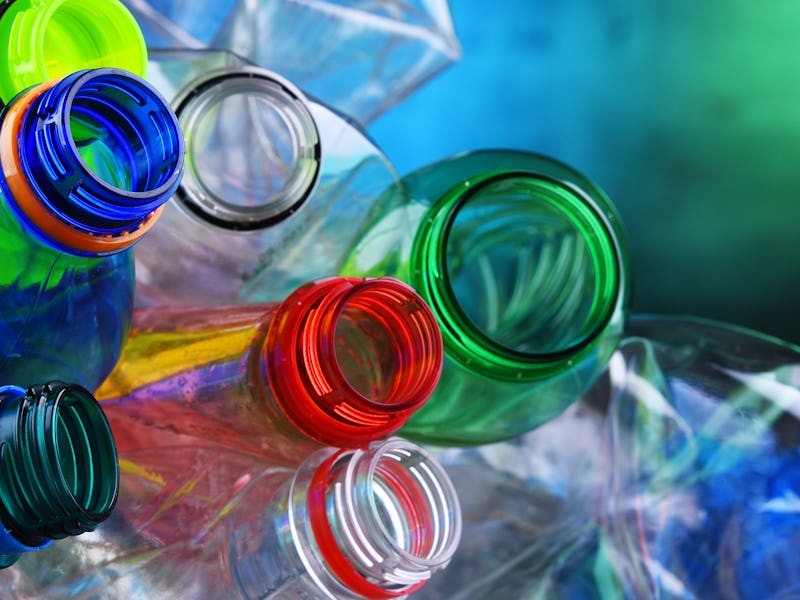
Dionisios G. Vlachos has plastic on the mind. The stuff fills up landfills, but finding a second life for it seems like a fool’s errand.
Vlachos compares it to building a house: “It’s difficult to build a house and it’s easy to smash it apart,” he tells Inverse. “This is the reverse. Plastic is very easy to make and difficult to break apart.”
The problem is Americans love plastic, generating more than 14.5 million tons of plastic containers and packaging alone in 2018, according to the EPA. While it’s easy to refine crude oil into the long strands of carbon necessary to make plastic bags and water bottles, it’s complicated and inefficient to reverse the process or to find an efficient afterlife at all. There’s a reason China stopped buying the world’s plastic waste a few years ago, and these days that means that most of our “recyclable” plastic ends up in landfills.
It’s not that it’s impossible to recycle plastic back into oil and then to other useful products like gasoline (or even other types of plastic.) The issue is doing that in a way that doesn’t burn more energy than you’re saving. It doesn’t do any good to turn a bunch of plastic bottles into gasoline if it takes more fuel to recycle it than it creates in the process.
Vlacho, a professor of physics at the University of Delaware, may have found a way to change it all. In a new study in Science Advances from Vlacho’s team may have finally cracked the code to cracking plastic. Literally.
What’s new — Figuring out a way to create any number of useful fuels — gasoline, jet fuel, diesel, and even more advanced lubricants like motor oil — from plastics in an efficient way is a bit of holy grail for energy scientists.
“This is the first technology that’s able to take the most difficult plastics and recycle them into something really useful,” Vlachos says to Inverse. “It’s the best way to recycle single-use plastics and packaging like polyethylene and polypropylene.”
Current refineries can easily create plastic, converting energy-dense oil into the long-strings of carbon necessary to make light-and-strong plastic bags or water bottles. But we can’t really reverse that process.
It is possible to burn plastic of course. You can throw it into a fireplace, and it’ll create heat. But it also creates tons of pollution (which is both inefficient and gross), and it takes a huge amount of plastic to create useful amounts of heat. So how can low-energy-density plastic turn back into high-energy-density oil?
The promise of recyclable plastic hasn’t panned out — leaving much of it in landfills.
How it works — “It’s a refinery in reverse,” Vlachos says. His method uses two readily available components, zeolite — which, among other things, is used to refine crude oil into gasoline — and platinum. Applying just zeolite to solid plastic breaks it down once, and then the process stops. The same is basically true for platinum. One catalyst or the other on its own is ineffective, but by combining platinum and zeolite as a dancing pair, “they do magic,” explains Vlachos.
The trick is “cracking” the long chains of carbon in plastic into short-C chains that are much more useful and versatile. It’s easy to “refine” oil into the long-C chains but very difficult to break them apart again. This is part of the idea, of course — you don’t want your plastic bag falling apart when you load it up with groceries. By putting both catalysts in a pressurized pot of plastic, Vlachos and his team found they could get very high yields of useful hydrocarbons even at relatively low temperatures.
In short, the platinum does the first crack, and then the zeolite goes to work, breaking it down further. Combining the acidity of zeolite with nanoparticles of platinum achieves high yields of liquid hydrocarbons (AKA oil) with very little solid byproduct.
They’re able to get a maximum liquid yield of 85 percent of the original material, with much of the rest off-gassed, leaving behind little in the way of solids. According to the study, “the catalyst is active in converting the most abundant plastic waste components, including HDPE, PP, polystyrene (PS), layered PP-PE-PS composites, and everyday plastic bags, bottles, etc.”
Adjusting the ratio of the two catalysts allows for optimization of the resulting mixture to create different fuels, including anything from jet fuel to gasoline to diesel. “The magic is in the materials,” says Vlachos. “Put the catalyst in the cooking pot, put the plastic in, pressurize it, and you get oil out.”
He says it would take something like 300 half-liter water bottles to create enough oil to make a gallon of gasoline — or two pickup truck beds stuffed full of water bottles to fill one gas tank.
What's next — A patent was filed last year for the process, and additional research is being done, but Vlachos says successful commercialization could be achieved within five to 10 years. “If you try to do it overnight, it won’t happen,” he says, noting that eliminating impurities like food waste on recycled plastic will be critical.
Millions of tons of plastic are sitting around in landfills, with millions more being generated every year. If there’s an energy-efficient way to recapture all that carbon and put it to good use, you can be sure that the world’s energy companies will be taking a hard look at the process and whether you’ll be able to use a bunch of empty water bottles to create your next gallon of gasoline.
Abstract: Single-use plastics impose an enormous environmental threat, but their recycling, especially of polyolefins, has been proven challenging. We report a direct method to selectively convert polyolefins to branched, liquid fuels including diesel, jet, and gasoline-range hydrocarbons, with high yield up to 85% over Pt/WO3/ZrO2 and HY zeolite in hydrogen at temperatures as low as 225°C. The process proceeds via tandem catalysis with initial activation of the polymer primarily over Pt, with subsequent cracking over the acid sites of WO3/ZrO2 and HY zeolite, isomerization over WO3/ZrO2 sites, and hydrogenation of olefin intermediates over Pt. The process can be tuned to convert different common plastic wastes, including low- and high-density polyethylene, polypropylene, polystyrene, everyday polyethylene bottles and bags, and composite plastics to desirable fuels and light lubricants.
By the way, if you liked this article, you’ll love my weekly car review newsletter PRNDL. Click here to subscribe for free on Substack. I’ll even answer your new car questions!