Tesla's Semi took too long — so these truckers built their own version
Musk keeps delaying Semi production, but you could soon take any old 18-wheeler and turn it hybrid.
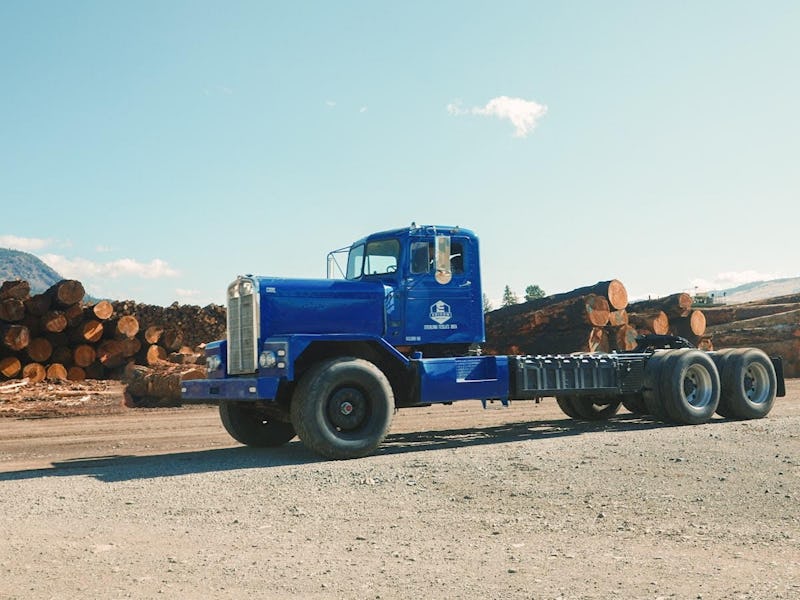
To Chace Barber, the semi-truck of tomorrow doesn’t look like Tesla’s super-sleek rendition, a battery-powered streamlined spaceship on 18 wheels. Instead, he thinks the future should borrow from the past: Barber wants to trick out a long-nose 1962 Kenworth for the electric era.
He recently went viral with a TikTok showing off his creation. “It’s been five years … since we put our deposit down on that Tesla electric semi,” he says in the clip. “Now, a bunch of TikTok truckers built their own electric truck in about six months. What’s taking so long, Tesla?”
Musk announced the Tesla Semi in 2017 and promised it would be ready to ship by 2019, prompting companies to reserve models ahead of time. He has continued to push back that deadline, and it wasn’t until earlier this month that customers learned they will (allegedly) begin receiving their sought-after vehicles later this year. But Barber is done waiting.
A DIY semi makeover
Although the retrofitted truck still burns diesel fuel, Barber says it uses far less than the hulking engine inside most 18-wheelers.
To get a head start on Tesla, Barber and his crew started a company called Edison Motors in Merritt, Canada. On September 9, they plan to unveil their vehicle to the world.
The vehicle in question: a hybrid electric truck with an onboard diesel generator that propels the truck’s motors and sends it speeding down the highway, no diesel engine required.
By electrifying older vehicles, the Edison approach circumvents the long wait for all-electric models — and who knows when Tesla will actually deliver.
“Everything about this truck tells you it should be loud and noisy. Driving it is the most surreal thing.”
Although the retrofitted truck still burns diesel fuel, Barber says it uses far less than the hulking engine inside most 18-wheelers. In the meantime, it can provide many of the perks of full electrification, such as lower fuel costs and plenty of raw power.
And while Barber didn’t provide an exact estimate, he claims it offers far better mileage than old-school trucks.
It also makes for eerily silent driving. After all, diesel engines produce the roaring sound you hear on the road when passed by a hefty semi.
“I've driven a Tesla a few times, and it's weird to me still that that car makes no noise when you step on the throttle,” Barber tells Inverse. “But when you hop into a Tesla, everything about that car tells you, ‘Hey, this is a modern electric car.’ When you hop into our truck, it's a 1960s logging truck. Everything about this truck tells you it should be loud and noisy. Driving it is the most surreal thing.”
An off-the-grid idea
Edison Motors will help truckers turn vintage Kenworths like the one shown here, or any old truck, into an electric hybrid.
Just a few years ago, Barber was working as a truck driver in Canada to put himself through college. At the time, he dreamed of building solar energy projects. But when he realized that goal was pretty costly, he and his business partner Eric Little came up with a plan B: They used the last $4,000 left from their student loans to buy a semi from the 1960s and haul heavy equipment, such as generators, all over British Columbia.
On one of those long trips, Barber and company visited Halfway River, a First Nations community in Canada’s icy northern regions. Because it’s isolated from the power grid, locals source electricity by burning diesel in a generator.
They needed a large, 95-kilowatt motor to meet peak demand, typically when everyone came home from work and started using lots of energy. While he was in town, Barber realized the community could get by with a much smaller generator (just 30 kilowatts’ worth of power) if they stored energy in a battery bank during periods of lower demand.
Edison’s retrofit kit would allow truckers to turn any older truck electric, and someday to sell its own Edison-branded trucks.
The eureka moment: Barber and company realized the same principle could hold true for a big rig. Semi-trucks carry huge diesel engines, around 15 liters, to move the weight of the truck and its load. But they don’t need all that power all the time.
“You need a lot of energy to kind of get that inertia going and build up your momentum,” he says. “But once you're at cruising speed, you don't need much.”
The Edison Motors guys retrofitted their 1960s machine with electric motors that drive the wheels, a battery system to send the power to those motors, and a diesel generator that whips up the energy that’s then stored in the battery.
This setup allows Barber and company to use a 6- or 9-liter diesel generator and ditch a traditional engine that’s around twice as big, delivering more than enough electric power while slashing the truck’s carbon emissions.
Once they can prove the prototype works, Edison plans to sell a retrofit kit that would allow truckers to turn any older truck electric. Someday, the company may even sell its own Edison-branded trucks.
Sexier solutions down the road
After years of delays, Tesla will allegedly start shipping its Semi by the end of this year.
Today, greener trucking is easier than ever, says Timothy Lipman, co-director of the Transportation Sustainability Research Center at the University of California, Berkeley.
Battery electric propulsion has jumped from cars to pickup trucks like the Ford F-150 Lightning and Rivian R1T, and is now poised to move into commercial vehicles including Amazon delivery vans and Tesla semi-trucks.
And hydrogen could really rev things up. Two decades ago, researchers considered hydrogen fuel cells to power just the supplemental power units in a heavy-duty diesel truck.
But now, because of a major improvement in fuel cell power density, hydrogen could even power the whole truck, Lipman says. That’s why some new future-focused startups have garnered heaps of investment money by promising semi-trucks powered by hydrogen fuel cells.
For now, he sees some advantages in the Edison hybrid approach. “It makes sense, and should result in some fuel savings,” Lipman says, though you’d get even more savings by using fuel cells to power a truck, or a battery setup that draws its power from renewable sources.
Plenty of people were ready to support a grassroots outfit like Edison and its practical, if unsexy, solution for the electrified truck.
Barber doesn’t disagree. But to him, that’s not the point. Ballyhooed battery and hydrogen startups that promise a leap into the technological future suck up attention and venture capital, but he wanted to fill an overlooked void: Build an electric truck with only parts he could get in his local parts store in a town of a few thousand people.
It turned out that plenty of people were ready to support a grassroots outfit like Edison and its practical, if unsexy, solution for the electrified truck, Barber says. Once people realized the deadpan Canadian wasn’t joking about starting his own company, Edison raised hundreds of thousands of dollars in a few days and has a lengthy list of people lined up to support a crowdfunding campaign.
“They're excited about this bridge technology,” he says. “To people saying like, oh, the excitement isn't there — it's there, but it's coming from the people that use the equipment, not from the tech sector.”
Barber argues that the Edison approach speaks to truckers, especially those who love the look of the traditional semi that hasn’t changed in a half-century and worry about the range issues of going fully battery-electric.
“We're saying, ‘Hey, you still keep your truck that you've had for the last 10 years’ ... And the response is like, ‘Whoa, hold on. I can keep my 1990s long-nose Peterbilt and still have the advantages of the high torque, bigger power, better mileage? Finally. We're so on board.’ [In this way], we've convinced so many people that electric is a good way of doing it.”
This article was originally published on